Elektronik imalat endüstrisinde çelik hasır temizliği, SMT üretim sürecinin "görünmez yaşam çizgisidir" ve lehim pastası baskısının doğruluğunu ve PCBA performansını doğrudan belirler. Veriler gösteriyor ki Lehimleme hatalarının 35%'si eksik şablon temizliğinden kaynaklanmaktadırve yanlış temizleme yöntemleri ekipman arızasına, malzeme israfına ve hatta güvenlik kazalarına neden olabilir. Bu makale, Dezheng Akıllı Temizlik Sisteminin teknik avantajlarını DEZ-C730 tam pnömatik şablon temizleme makinesi milyonlarca dolar zarara neden olabilecek beş temizlik kör noktasını derinlemesine incelemek ve risklerden kaçınmanıza yardımcı olmak için.
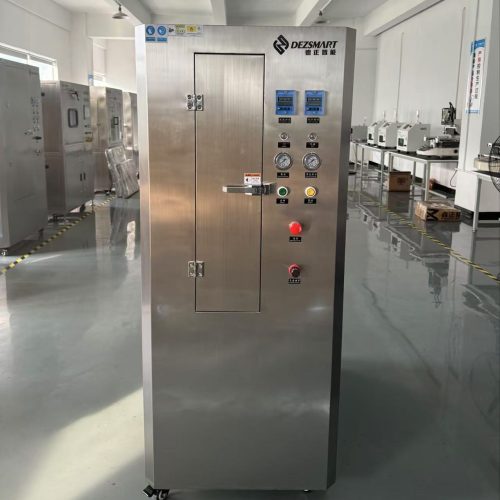
(DEZ-C730钢网清洗机)
1. Mikro gözenek kalıntısı: 0,1 mm'den küçük kirlilikler kalitenin "görünmez katili" haline gelir.
▎Ölümcül Risk
Şablonun çapı tipik olarak 0,1 ile 0,5 mm arasındadır. Yeniden akış lehimlemeden sonra kalan lead içermeyen lehim pastası reçinesi ve flux, mikron düzeyinde kristaller oluşturacak ve bu da bir kalite riski haline gelecektir:
- Fonksiyonel arıza: 0,05 mm seviyesindeki kalıntılar lehim pastası sızıntısına/köprülemesine neden olarak soğuk lehimlemeye ve bileşen kısa devrelerine yol açar (otomotiv elektroniği fabrikası müşterilerimizden biri ayda ortalama 120.000 PCBA kısa devresine sahiptir ve yeniden işleme maliyeti 800.000 yuan'ı aşmaktadır);
- Uzun süreli korozyon: Artık organik madde çelik hasır alt tabakaya nüfuz ederek nikel/gümüş kaplamanın korozyona uğramasına neden olur ve ürün ömrünü etkiler.
▎DEZ-C730 Teknolojik Atılım
360° dönen çift taraflı izobarik jet teknolojisi sayesinde mikron düzeyinde temizleme gücü elde edilir:
- Yüksek basınçlı penetrasyon: 0,45-0,6 MPa'lık pnömatik su basıncı, 20 m/s hızla ağa çarparak moleküler düzeyde yapışmayı ortadan kaldıran su akışını iter;
- Üç aşamalı filtreleme garantisi: 5 μm + 1 μm ince filtreleme (1 mm birincil filtreleme ile), kalay cürufu ve reçine partiküllerinin 99,9%'sini keserek ultra ince 0,02 mm gözenekli temizlik sağlar.
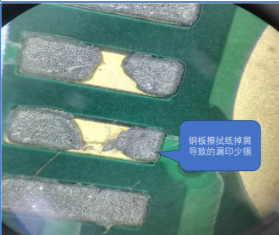
(lehim pastası sızıntısı)
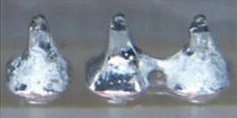
(Bridging)
2. Gerilim Arızası: Yetersiz temizleme basıncı çelik ağın ölümcül şekilde deforme olmasına neden olur.
▎Anahtar Detaylar
Çelik ağ gerginliği (standart değer 35-50 N/cm) baskı doğruluğunun birincil göstergesidir. Geleneksel temizleme yöntemleri risk taşır:
- Mekanik Hasar: Yüksek frekanslı ultrasonik titreşim/manuel fırçalama 15%'lik gerilim zayıflamasına neden olur ve lehim pastası kalınlığı sapması ±20%'yi aşar;
- Dava Uyarısı: Tüketici elektroniği fabrikası müşterilerimizden biri, milyonlarca cep telefonu anakartı üzerindeki lehim pedlerinin kaymasına neden olan düzensiz çelik hasır gerginliği nedeniyle 1,2 milyon RMB doğrudan zarara uğradı.
▎Ekipman Avantajları: Hasarsız Temizlik Tasarımı
DEZ-C730 tamamen pnömatik çelik hasır temizleme makinesi, nozulu çalıştırmak için bir hava motoru kullanır ve iki ana koruma sağlar:
- Sabit Basınçlı Püskürtme: Basınç sensörü, eşit püskürtme basıncı ve temizlikten sonra 5%'den daha az gerilim dalgalanması sağlamak için gerçek zamanlı olarak izler;
- Temassız Temizlik: Mekanik sürtünmeyi önler, çelik ağın yüzey kaplamasını ve gerilim yapısını korur ve QFP/BGA gibi yüksek hassasiyetli baskı gereksinimlerini karşılar.
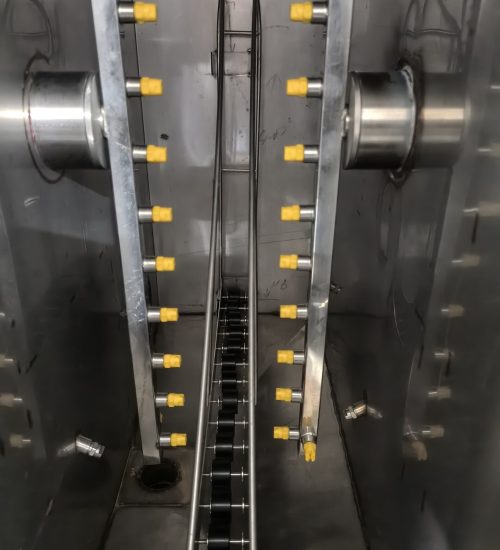
(Temizlik odası)
3. Solvent atıkları: Kaba temizlik, sarf malzemelerinin "dipsiz bir kuyuya" mal olmasına neden olur.
▎Atık kaynakları
Geleneksel temizlik modeli neden "para yutan bir canavar" haline geldi?
- Açık tank: Bir seferde 500-1000L sıvı tüketilir ve kirlilikler filtrelenmez, sıvıyı 2-3 gün içinde etkisiz hale getirir;
- Manuel çalıştırma: Deneyimlere dayanarak, aşırı solvent çelik ağın kenarına sızar ve atık oranı 30%'yi aşar;
- Gerçek veriler: OEM müşterilerimizden birinin yıllık temizlik maddesi maliyeti 650.000 RMB'ye kadar çıkmaktadır, bu da ayda iki ek device satın almaya eşdeğerdir.
▎DEZ-C730 Tam Pnömatik Şablon Temizleme Makinesi Maliyet Kontrol Çözümü Üç aşamalı Filtrasyon Sirkülasyon Sistemi:
Filtrasyon seviyesi | Hassasiyet | Yakalanan safsızlıklar | Temel değer |
---|---|---|---|
1. seviye birincil filtre | 1mm | Kalay cürufu, etiket döküntüleri | Memeyi koruyun ve tıkanmayı önleyin |
2 aşamalı ince filtreleme | 5μm | Lehim pastası parçacıkları, gümüş pasta | Temizleme sıvısının temizliği 98%'den daha yüksek seviyede tutulur |
3 aşamalı nanofiltrasyon | 1μm | Reçine kalıntısı, reçine | Sıvı ömrü gelenekselin 5 katına kadar uzatıldı |
4. Güvenlik riskleri: Elektrikli ekipmanlar atölyede bir "saatli bomba" haline gelir.
▎Güvenlik Kör Noktaları
Solvent bazlı temizlik maddeleri (IPA gibi) yanıcı ve patlayıcıdır (parlama noktası 12°C) ve geleneksel elektrikli ekipmanlar gizli riskler oluşturur:
- Kıvılcım ateşleme: Motor sürtünmesi, kolayca solvent buharı patlamalarına neden olabilen statik elektrik / kıvılcım üretir (2023'te, bir SMT fabrikası ekipmandaki kısa devre nedeniyle alev aldı ve üretim hattı üç hafta boyunca kapatıldı ve 2 milyon yuan'ın üzerinde bir kayıpla sonuçlandı);
- Elektrik çarpması tehdidi: Sızıntı koruması başarısız olduğunda, operatör doğrudan elektrik çarpması riskiyle karşı karşıya kalır.
▎Kendinden Güvenli Tasarım: Tamamen Pnömatik Tahrik
DEZ-C730 tamamen pnömatik şablon temizleme makinesi, elektrik tehlikelerini kaynağında ortadan kaldırır:
- Üç büyük güvenlik garantisi:
- Güçsüz çalışma: Motor/devre olmadan yalnızca basınçlı havaya (0,45-0,6 MPa) dayanır ve patlamaya dayanıklı standartları karşılar;
- Kapalı koruma: Tamamı paslanmaz çelik gövde + solvent buharlaşmasının yangın kaynaklarıyla temas etmesini önlemek için kapalı temizleme kabini;
- İnsan-makine izolasyonu: Tek tuşla çalıştırma, temizlik maddeleriyle manuel temas gerektirmez, iş sağlığı risklerini azaltır.
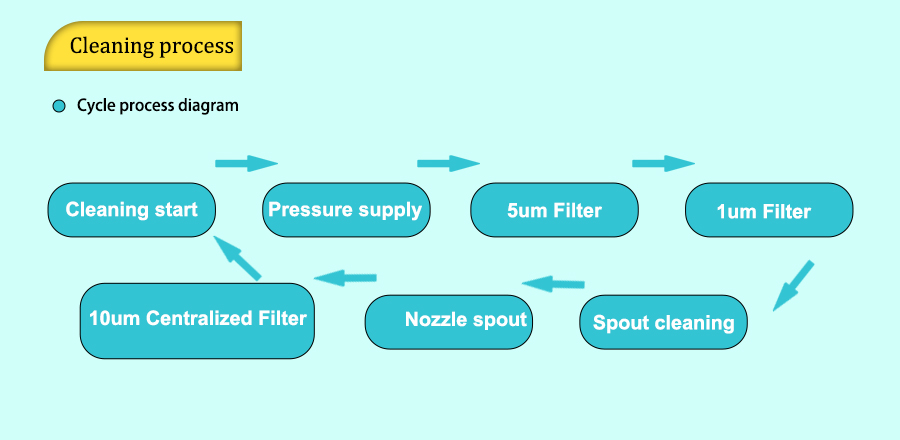
(DEZ-C730 Temizleme işlemi)
5. Uyum Açığı: VOC emisyonlarının aşılması çevre koruma cezalarına yol açar.
▎Önemli Uyumluluk Noktaları
Çevresel düzenlemeler giderek daha sıkı hale geliyor ve geleneksel temizleme modelleri çifte baskıyla karşı karşıya kalıyor:
- Siyasi kırmızı çizgiler: AB REACH VOC emisyonlarının 100 ppm'in altında olmasını gerektirmektedir ve Çin standartları açık buharlaşmayı yasaklamaktadır (standardın 3 ila 5 kat aşılması 500.000 ila 1 milyon yuan para cezası ile sonuçlanacaktır);
- Gerçek vaka: Bir şirket, yıllık emisyon standartlarını aştığı için 580.000 RMB para cezasına çarptırıldı ve düzeltme için 30 gün boyunca üretimi askıya alması istendi.
▎Çevre Koruma İyileştirme Planı
DEZ-C730 tam pnömatik şablon temizleme makinesi, donanım tasarımı sayesinde çevresel uyumluluk sağlar: Emisyon Kontrol Teknolojisi:
- S-tipi egzoz borusu, 50 ppm, 50%'nin altındaki VOC konsantrasyonlarını yasal standarttan daha iyi kontrol eder;
- Kapalı temizleme haznesi tasarımı, geleneksel ekipmana kıyasla sıvı buharlaşmasını 60% oranında azaltır.
-- Şablon Temizliğinin "Altın Kuralı": "Yangın Söndürme "den "Önleme "ye --
▎Ekipman Seçiminde Üç Faktör
- Önce Güvenlik: Tamamen pnömatik tahrik (DEZ-C730 gibi), elektrik kıvılcımı veya statik elektrik riskini ortadan kaldırır;
- Doğruluk Garantisi: 360° döner enjeksiyon + üç aşamalı filtrasyonu destekler, 750 mm × 750 mm çelik ağ için uygundur;
- Kontrol Edilebilir Maliyet: Temizleme sıvısı geri dönüşüm oranı >95%, tek parti sıvı tüketimi ≤200 ml (su/solvent bazlı temizlik maddeleri için yaygındır).
▎Süreç Standardizasyon Yönetimi
- Standart süreç oluşturun: yıkama 2-4 dakika + kurutma 2-5 dakika (geleneksel işlem);
- Düzenli kalibrasyon: Çelik ağın gerginliğini her ay kontrol edin (dalgalanma <5% olmalıdır).
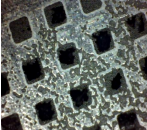
(Temizlemeden önce)
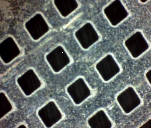
(Temizlikten sonra)
Başarı ya da başarısızlığı ayrıntılar belirler ve temizlik verimliliktir.
Elektronik üretiminin "mikrona kadar yarışında", şablon temizlemedeki her hata büyütülebilir ve milyonlarca dolarlık kayıplara dönüşebilir. Dezheng Intelligent DEZ-C730 tam pnömatik şablon temizleme ekipmanı, eksiksiz proses güvenliği tasarımı, mikron düzeyinde temizleme hassasiyeti ve akıllı filtreleme sistemi ile işletmeler için "risk önleme ve kontrol + verimlilik iyileştirme" gibi ikili bir bariyer oluşturur. Temizlik sürecinizi hemen iyileştirin ve ayrıntıların dipsiz bir maliyet çukuru yerine kalite çukuru haline gelmesine izin verin.