Welcome to DEZ
Dry Ice Cleaning Machine
- Global support
- Fast response
- Customer focus
Dry Ice Cleaning Machine
Dry Ice Cleaning Machine uses CO₂ pellets to blast away contaminants without abrasion or residue. It’s perfect for cleaning delicate components, stencils, and conveyors. The non-toxic, water-free process reduces downtime, enhances cleanliness, and aligns with eco-friendly practices. Easy to operate and maintain, it’s a reliable solution for keeping SMT equipment in top condition.

Popular Product
-
Dry Ice Cleaning Machine
DEZ-C7320 Inline Dry Ice Cleaning Machine
-
Dry Ice Cleaning Machine
DEZ-C7310 Dry Ice Cleaning Equipment
-
Dry Ice Cleaning Machine
DEZ-C1650 Dry Ice Cleaning Machine
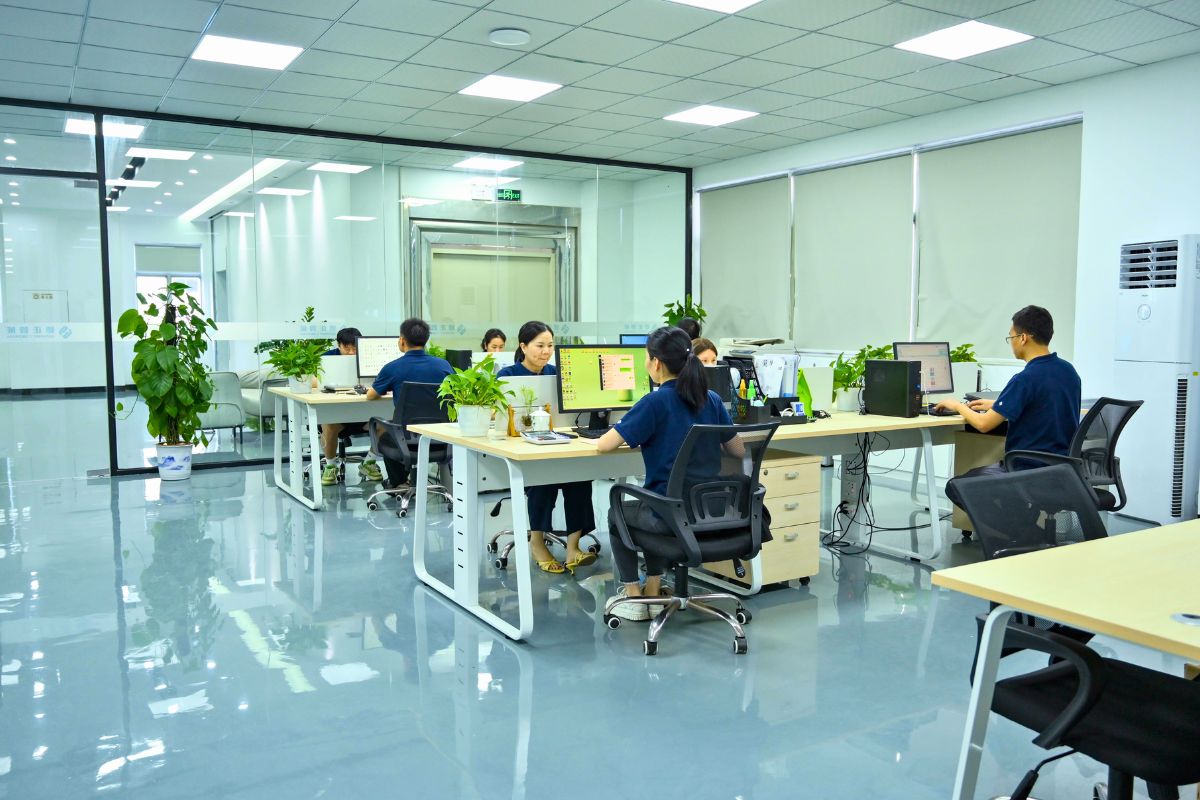
Why Choose DEZ
At DEZ SMT, we pride ourselves on being more than just a supplier of advanced SMT equipment—we are your partner in achieving manufacturing excellence. With a strong commitment to innovation, quality, and customer satisfaction, we provide solutions that help our customers stay ahead in the competitive world of PCB assembly.
Industry Expertise
Our R&D-focused approach ensures state-of-the-art solutions that keep pace with evolving industry demands.
Quality and Efficiency
Every machine is built to deliver reliable, consistent performance, ensuring that your production line operates smoothly and efficiently.
Global Support
Backed by a worldwide service team, we provide local technical support, training, and maintenance to ensure seamless integration.
Customized Solutions
Whether you're a startup or an industry leader, we tailor our solutions to fit your production needs.
Ready to get the right machine for your project?
Our team of experts is here to help you in selecting the best solutions for your needs. Please feel free to reach us for support.
Frequently Asked Questions.
DEZ provides high-performance SMT solutions, including automated cleaning machines, selective wave soldering systems, X-ray inspection equipment, and SMT peripherals. Our machines are designed for precision, efficiency, and reliability in electronics manufacturing.
Yes, we specialize in providing tailored solutions to meet the specific needs of each customer. Our team works closely with you to understand your production requirements and design a solution that maximizes efficiency and productivity. This includes customizing equipment configurations, optimizing dispensing patterns, and integrating our machines into your existing production line.
We provide comprehensive support services, including installation, training, technical support, and preventative maintenance. Our goal is to ensure that your equipment operates at peak performance throughout its lifespan. Our global support network ensures that you receive timely assistance, no matter where your facility is located.
Yes, we offer equipment demonstrations to help you better understand the capabilities and performance of our products. You can schedule a demo at our facility or request a virtual demonstration. Please contact our sales team to arrange a demo session that fits your schedule.
You can order spare parts directly through our website or by contacting our customer service team. We maintain a large inventory of genuine, high-quality spare parts to ensure fast delivery and minimize downtime. If you need assistance in identifying the right part, our team is here to help.